|
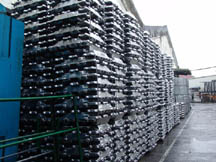
1.
Concept One wheels start life out as raw slabs of refined aluminum alloy
ingots. These are specifically formulated for alloy wheel manufacturing
as dictated by world stndards such as JWL and VIA. |
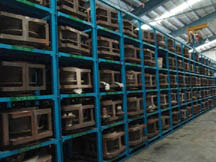
2.
As demand dictates, molds have to be pulled from Concept One's vast inventory
of wheel molds. |
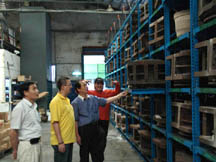
3.
The molds in the factory total over 500, with a specific mold for a specific
size of wheel. One design can have as many as 10 molds for sizes 13" -
22 "
|
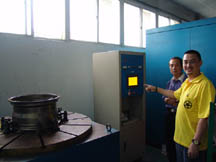
4.
One of the tests is the cornering force test, where the wheel is clamped
and spun while sideways force is applied to test the shearing forces applied
to the wheel. OEM standards dicvtate that wheels must survive 100,000
cycles. Concept One tests their wheels for 300,000 cycles. |
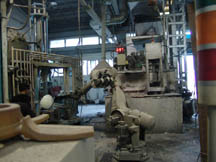
5.
As the aluminum ingots are being melted in a universal melting furnace,
the molds are then placed on various casting machines on. A robotic arm
then scoops molten aluminum and pours them into the different casting
machines. The whole process is timed perfectly for maximum efficiency.
|
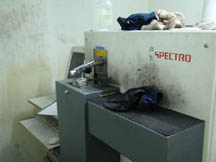
6.
VIA and JWL standards dictate that wheels must be made to the specifications
of A356.2 which is composed of aluminum and trace amounts of silicon,
magnesium and strontium. A Spectro photo spectrum analyzer is continualy
used during the melting process to determine the precise composition of
each batch of wheels to make sure they conform to these standards. The
spectrum analyzer is also used to carefeully monitor amounts of iron to
make sure that the concentraction is less the 0.1%.
|
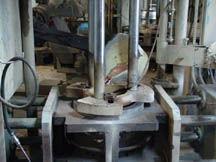
7.
Here, the robotic arms pours molten aluminum into a mold on the casting
machine.
|
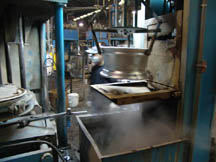
8.
A robotic grasper then lifts the wheel...
|
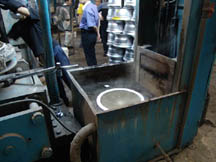
9.
...and dips it in water to fast cool and quench the wheel.
|

10.
Freshly casted wheels are then stacked to be shipped to the next step.
|
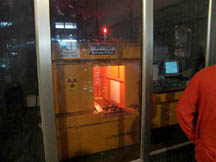
11.
Before each wheel is approved for machining, Fresh batches of wheels are
subjected to X Rays to view any possible hollow spots inside the wheel.
Wheels are accepted when there are no air pockets detected inside the
casted wheel.
|
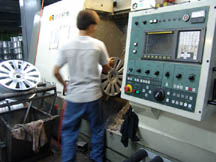
12.
Wheels come off the mold without any holes. They are then placed in a
CNC machine that automatically machines off extra casting flashings. Another
CNC machine then drills the appropriate bolt patterns for the various
cars.
|
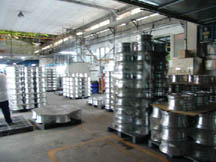
13.
Once again, batches of machined wheels are stacked together. |
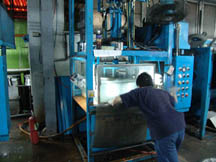
14.
The wheels then undergo a leak test to determine if there are minute pinholes
in the casting. Wheels with leaks are automatically rejected. |
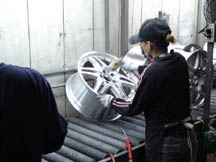
15.
Each wheel undergoes de-burring and surface prepapration in readiness
for painting. |
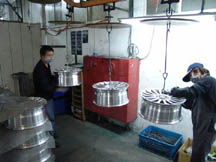
16.
Wheels are then put on a moving conveyor and gets a powder coat to ensure
the adhesion of the paint to the wheel. |
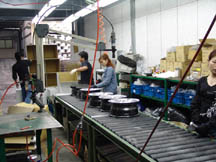
17.
Each wheel is then subjected final quality control inspection to check
for imperfections. Finished wheels are then put on a conveyor in the packing
area. |
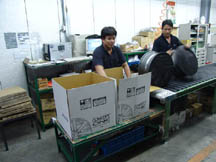
18.
The face is then wrapped with cloth and placed in boxes.
|
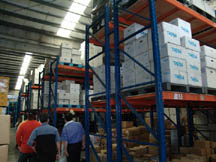
19.
Packaged wheels are then stored in the vast warehouse. |
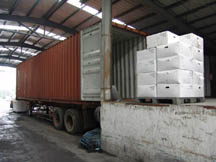
20.
They are then delivered to the container for worldwide shipment. |
|
|
|
|
|
|
|